What is Amazon Project P.i? How is it used AI to spot defects before dispatch? 🤖
Amazon's Project P.I. employs AI and computer vision to enhance product quality, improve customer satisfaction, and streamline operations, revolutionizing defect detection in fulfilment centers.
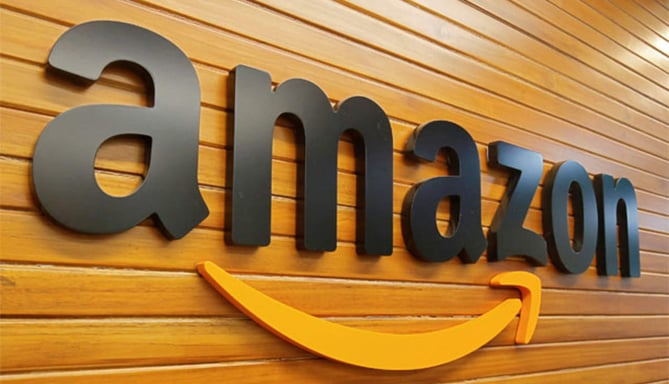
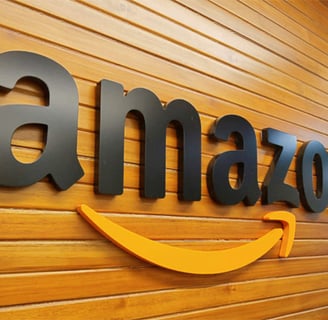
Amazon "Project P.I." (short for "private investigator"), an initiative leveraging the power of computer vision and artificial intelligence (AI). This project aims to ensure that every product dispatched from Amazon’s fulfilment centres is in perfect condition, significantly reducing the instances of customers receiving damaged or incorrect items.
How Project P.I. Works
Project P.I. operates within Amazon’s fulfilment centres across North America. The system employs generative AI and computer vision technologies to meticulously scan millions of products daily, identifying defects that might escape human eyes.
Project P.I. is the imaging tunnel, a sophisticated setup where each product is photographed and analyzed before dispatch. The AI-driven system evaluates these images to detect various types of defects, such as physical damage, incorrect colours, and mismatched sizes. This process is incredibly efficient, handling the massive volume of items Amazon processes each day.
When the system detects a defect, the item is immediately flagged and isolated for further inspection. This step ensures that problematic products do not reach customers, maintaining high standards of quality and customer satisfaction.
Enhancing Manual Inspections
Despite the sophistication of Project P.I., it is designed to complement, not replace, human workers. Amazon associates review the flagged items to determine the best course of action. Depending on the nature of the defect, items may be:
Resold at a Discount: Slightly damaged but functional products can be sold at a lower price on Amazon’s Second Chance site.
Donated: Usable items that cannot be sold may be donated to various charitable organizations.
Repurposed: Items that cannot be sold or donated might be recycled or repurposed, reducing waste.
This system acts as an additional layer of quality control, augmenting manual inspections and ensuring thorough scrutiny of all products.
Amazon’s VP Dharmesh Mehta highlights the customer-centric nature of Project P.I.:
“We want to get the experience right for customers every time they shop in our store. By leveraging AI and product imaging within our operations facilities, we are able to efficiently detect potentially damaged products and address more of those issues before they ever reach a customer, which is a win for the customer, our selling partners, and the environment.”
Sustainability Efforts
Project P.I. is not just about maintaining product quality; it also plays a crucial role in Amazon’s sustainability initiatives. By preventing damaged or defective items from reaching customers, the system helps in:
Reducing Returns: Fewer defective products mean fewer returns, which in turn reduces the environmental impact associated with return shipping.
Minimizing Waste: By identifying and addressing defects early, Amazon can reduce the amount of packaging and product waste.
Lowering Carbon Emissions: Efficient defect management helps lower the carbon footprint associated with transporting returns and replacements.
Kara Hurst, Amazon’s VP of Worldwide Sustainability, elaborates on this aspect:
“AI is helping Amazon ensure that we’re not just delighting customers with high-quality items, but we’re extending that customer obsession to our sustainability work by preventing less-than-perfect items from leaving our facilities, and helping us avoid unnecessary carbon emissions due to transportation, packaging, and other steps in the returns process.”
Investigating Root Causes with AI
In addition to detecting defects, Amazon employs a generative AI system equipped with a Multi-Modal LLM (MLLM) to delve deeper into the root causes of negative customer experiences. This system reviews customer feedback and analyses images from fulfilment centres to identify where and why errors occur.
For instance, if a customer reports receiving the wrong size of a product, the system can trace back through images and data to understand whether the error occurred due to mislabeling at the fulfilment centre. This analysis allows Amazon to address the root cause of the issue, preventing similar mistakes in the future.
Benefits for Selling Partners
Project P.I. also offers substantial benefits to Amazon’s selling partners, especially small and medium-sized businesses, which constitute over 60% of Amazon’s sales. By providing detailed defect data, Amazon helps these sellers to quickly identify and rectify issues, enhancing their product quality and customer satisfaction.
Conclusion:
The implementation of Project P.I. represents a significant advancement in Amazon’s fulfilment operations, blending cutting-edge technology with practical applications to enhance product quality, customer satisfaction, and sustainability. This initiative highlights Amazon’s commitment to leveraging AI and computer vision to create a more efficient and environmentally friendly supply chain.